- Home
- Products
- Double Backer
- l08-1-01
DOUBLE BACKER (18PCS OF STEAM CHESTS) - DF-12
- A. Heating Section:
- Steam chests: cast iron product, 150mm(H) x 600mm(W) x 1900mm(L) --- 18 pcs, surface with ground polish and chromed.
- Up-down adjustment of Air press operated by hydraulic device. (with hydraulic unit --- 1 pc.) FIG.2
- 4 section pressure adjustment device of air press adjusted by air cylinder.FIG.1
- Steam pressure is divided into 4 sections and rear 2 sections are adjustable.
- Right and left adjustor of upper canvas belt --- 1 set.FIG.1
- Up-down adjustment gearboxes of air press --- 8 pcs.
- Main frame made of 15" channel steel.
FIG.1
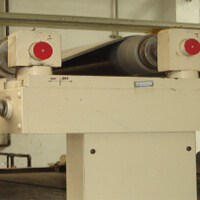
FIG.2
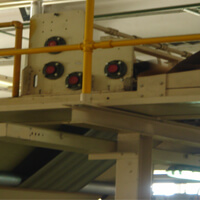
- B. Cooling Section:
- Upper weight rollers: Diameter 57mm, steel product --- 23 pcs.
- Lower guide rollers: Diameter 88mm, steel product --- 23 pcs.
- Tension adjustor of upper canvas belt --- 1 sets. (With hydraulic cylinder Dia. 80 x 300 mm ST. --- 2 pcs.)
- Tension controller of lower canvas belt --- 1 set.
- Main frame made of 12" channel steel.
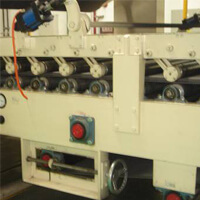
- 8-1. Cotton Belt:
- Imported product.
- Length: 8-9mm (T) x 1850mm (W) x 58M(L)
- Material: 100% Polyester.
8-2 AIR PRESS (13SET)
Advantages of AirPress
Higher production speed and output AirPress when compared with Weight Rolls and Thermo Bar has the capability of putting a very even adjustable pressure on the board. This ability enables the system to out perform all the competitors’ machinery across the whole flute range. Dramatic increases have been seen from the microflutes (E/F) up to Triple Wall.
Better board quality
a) By having the unique advantages of even pressure across the full width of the machine, coupled with the ability to adjust the loading, allows for greater controls for improving quality. Firstly, we can reduce the moisture content in the board. This is done by reducing the starch consumption and better removal efficiency. Dramatic improvements can be found in wash boarding problems and Delamination. The sheet coming out of the Corrugator is also more stable with an even moisture profile, reducing post warp problems. This stability gives you a flatter sheet with reduced waste. Caliper loss within the Double Facer is gone, as the system cannot crush the flutes. You will be delivering to the Converting area or the end customer a far better quality product. Flexo machines will run more consistently, no more fighting with adjustments to improve print or jam ups due to poor quality. b) The biggest gain is with warp control. You are now in complete control of the process which means that warp problems are addressed immediately. We achieve this by ensuring the board is held precisely onto the hotplate with the correct amount of starch. Evenly balanced moisture content between the liners is achieved and a firmer stable sheet delivered from the machine.
Less starch consumption
We achieve high starch reductions, operations show between 10 and 30%, due to the even pressure loading across the full width. This means that the flute is held positively against the liner, and then the heat is transferred efficiently creating the most effective bonding situation. No longer are you fighting plate distortion and uneven pressure loading by applying more starch.
Paper base weight and consumption of medium can be significantly reduced. Paper basis weight and medium can be reduced. With the loading system being very flexible, there is no crush or damage to the flute. The caliper entering the system, is the same at exit. This means that caliper and strength are maintained. FCT and ECT values increase accordingly, and this gives the user the option of keeping the higher strengths, or as in most cases, reducing the paper basis weights. As we already know, a caliper reduction/increase of 0.1mm
equates to a corresponding increase/decrease of 1.5 to 2.5% in weight. For 10,000,000 lin meters of paper, this equates to a potential of 150,000 to 250,000 lin meters.
Maintenance almost free
Maintenance is minimal on the system. There are no bearing to lubricate/replace, no spring adjustment, no shoe mechanism maintenance. The air sac is guaranteed for 3 years and the skid plates run for 10 years or more. Shorten hot plate and traction sections.
Shorten hot plate and traction sections
As the system operates more efficiently, the requirement for long hot plate and traction sections is removed. This equates to being able to run a Double Facer approximately ¾ the length of a standard, but with all the savings in quality, starch, efficiency (power/steam) and maintenance. 300m/min machines are running with 16 hotplates.
Auto operation linking with production management system
The Automatic Touch Screen control, can be linked with the plant anagement/scheduling system. 50 preset settings can be set up, allowing total hands off operation for the operator. This means that the system operates at optimum settings producing the best quality sheet at highest performance.
Thermal Deflection
Thermal deflection of hot plates surfaces while generally acknowledge is not well understood by most plant people.
It is difficult to monitor under running conditions which is the only way to determine the true dynamics of hot plate thermal deflection.
With acknowledgement to the dedicated few who were willing to crawl under a running double backer and read dial indicators, set up to measure steam chest deflection under varying conditions, the following graphs are provided to explain the phenomenon Figure No. 1 show the measure deflection in the first six hot plates of a typical corrugator operating in the single 160 to 180m/min (550 to 600 ft/min) range on single wall board.
With the transfer of heat from the top hot plate surface, it is “cooled” relative to the bottom surface, contracts and causes the surface to deform or “sag” as it is facer, gaining temperature, the rate of heat transfer declines as does the rate of cooling in the top surface of the hot plate resulting in less deflection in each hot plate moving down the double facer.
While the amount of deflection will vary slightly depending on the construction of the steam chest, and basis weight of the board being run, the deflection pattern remains fairly constant. Efforts to correct the “sag” by “stacking up” the steam chest in the middle are doomed to failure and may cause serious damage to the steam chest or side frames. The “sag” is not a structural problem where added support will correct the condition. It is a thermal differential between top and bottom surface which cause a differential expansion of the surfaces resulting in the deformation which can not be mechanically restrained.
Figure No. 2 shows the effect of board speed on deflection. In this instance, the measurements are all taken on a single steam chest, ( no. 4), with the corrugator speed being increased by 15m/min (50ft/min) increments are approximately 5 minute intervals beginning at 60m/min (200ft/min).
The hot plate surface deflection increases as the faster moving board removes more energy from the hot plate surface causing it to “cool” and a contract more.
Combining the hot plate surface dynamics shows in Figures No. 1 and 2, one can easily visualize the thermal deflection “valley” moving up and down the double facer in response to changes in corrugator speed, basis weight of the board, (double wall will pull considerably more energy hence the typical slower run speed), and moisture content. At some point, the hot plate surface is no longer in intimate contact with the board liner, the heat transfer rate falls off dramatically, as shown in Figure No. 3 and the corrugator speed must be slowed down to maintain board quality.
Efforts to maintain heat transfer and bonding by forcing the board in to intimate contact with the hot plate surface using addition or pressured weight rolls, even crowned, segmented or rubber covered rolls are marginal at best. They represent a “fixed” condition of concentrated loading trying to deal with a constantly changing surface deflection. Figure No. 4 demonstrates why parallel rolls are most often ineffective
and why edge crush, caliper loss, blisters and poor bonding problems are common place as efforts are made to increase corrugator speeds in to the 150-250 m/min (500-800ft/min) or better range. Keep in mind that loss of intimate contact as represented in Figure No. 3 with the 0.025mm (0.001”) air gap reduces heat transfer by approximately two-thirds.
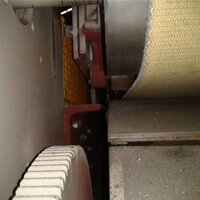
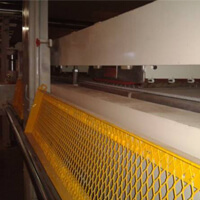
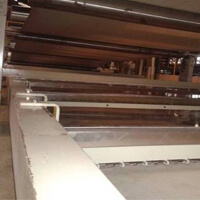
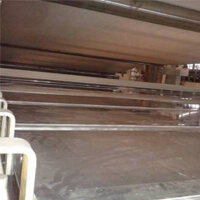
Sensor
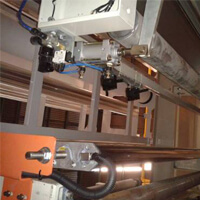
Sensor

Control panel
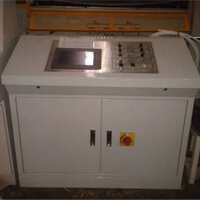
Blower
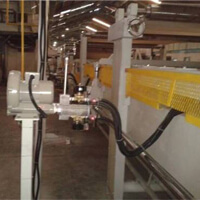